Centralized environment for managing PCB design data
Xpedition provides a fully integrated and centralized PCB design data management infrastructure, from initial system definition through the design process, to release, to manufacturing. Improve individual or team design with enhanced security, consistency, metric collection and process control.
Increased overall team productivity
Controlled access is available for project team members to both design and design status information. Collaboration management is facilitated for concurrent design, design reviews, release and IP management.
Reuse existing IP in the form of components and certified circuits for new products.
Reusing proven elements from previous designs through a library of certified circuits allows new product development teams to leverage past successes for the benefit of their latest generation of products.
Simplified enterprise library management
Manage library data from part request, to part creation of multi-discipline models, to library distribution with filtering and timely updates, to where-used analysis and collaboration, with enterprise administration to control security and enable 3rd party integrations. Enterprise-level library management seamlessly integrates multiple disciplines.
Seamless PLM Integration
Xpedition integrates with the electronic design supply chain and extended enterprise applications like PLM and ERP.
Direct access to comprehensive part intelligence
Xpedition integrates technical parametric information, alternates, and real-time component sourcing intelligence for 650 million+ parts, providing actionable insights at every stage of the design process and synchronization with part request workflows and PLM systems. Learn more about supply chain resilience.
Dive deeper into this topic
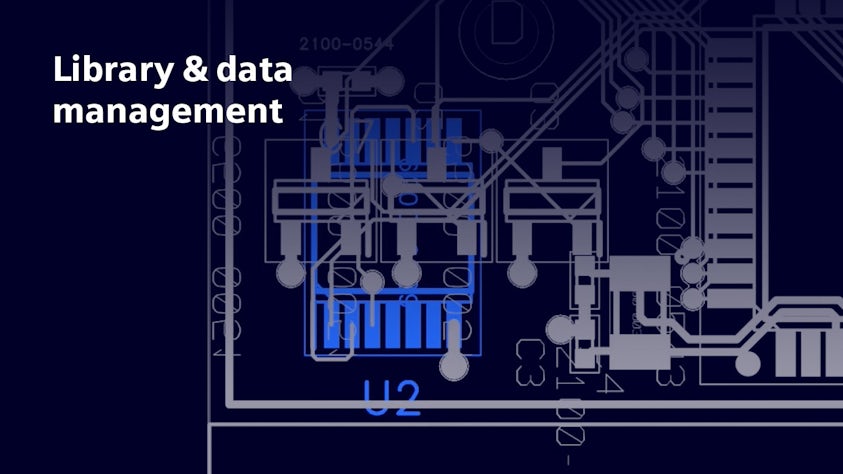
You want to establish internal guidelines and processes for library and design data management, that way you have an internal set of guidelines and rules in order to operate consistently. Read more in our library and design data management blog or listen to our library and design data management podcast.