Concurrent design for manufacturability saves time and cost
The further into the design process a problem is discovered, the more it costs to rectify. With Valor DFM analysis technology, anyone can run concurrent DFM analysis within Xpedition to locate problems, allowing for instant solutions during the design process. More than 1,000 checks are built in for full coverage.
Design for Manufacturing for flexible and rigid-flex circuits
Because nearly 30 percent of all electronics companies have flex and/or rigid-flex circuits within their product portfolios, it is important to include them in DFM. The materials and manufacturing processes are different for flex and rigid-flex circuits compared to conventional rigid boards, and Valor DFM analysis technology supports these different needs.
Automated DFM analysis
Valor NPI software from Siemens uses expert system logic to automate DFM analysis. High-quality automated DFM analysis is based on a combination of PCB technologies and manufacturing constraints. PCB technology can be automatically determined with intelligent design data.
For example, the copper weight of each layer is critical in the fabrication DFM analysis because of the etch compensation applied and, thus, resultant etch-back are going to vary based on the copper weight used. Letting the DFM software act on each of these constraints automatically saves engineering effort and delivers the desired results consistently for every user, regardless of their manufacturing expertise.
Accurate and validated data for PCB manufacturing
Intelligent data formats such as ODB++ and IPC-2581 enable efficient data exchange. These types of data formats facilitate intelligent communication from engineering to manufacturing and create a digital thread that spans from design to manufacturing, minimizing errors and providing a continuous feedback loop of information from manufacturing back to design.
Dive deeper into this topic
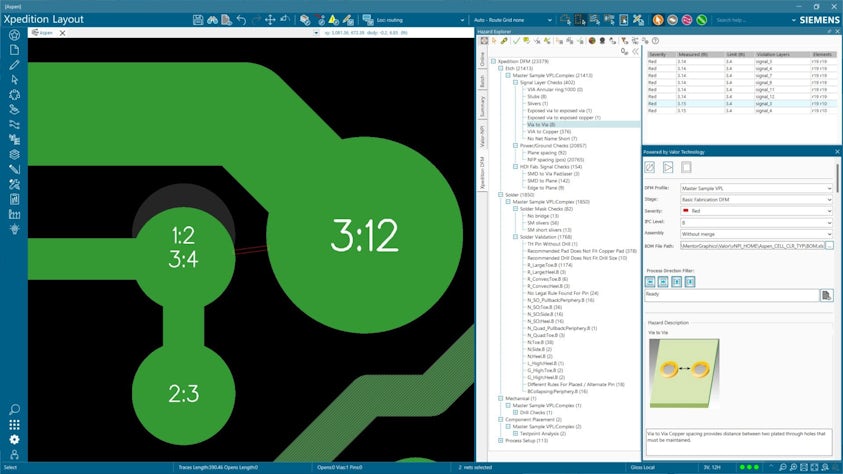
Data exchange should be bidirectional. By doing this, we enable lessons learned from manufacturing to be fed back to design/engineering. That bidirectional loop, or that data exchange, has to highest potential to positively influence the design. Learn more by reading our design and manufacturing collaboration blog or listening to our design and manufacturing collaboration podcast.