Multiple board outlines
With Xpedition, all you need to do to create a rigid-flex design is to draw the multiple board outlines and assign layer stack-up to each. Each board outline is given a name so that it can be easily identified when outlines overlap partially or completely.
Bending and folding
The key reason for making a flex design is so that it can be bent or folded. Xpedition includes a draw object, called a “bend area,” the location of which defines where the bend happens.
Route along curving boards
When you have a curving flex cable and as many signals that can fit with a tight squeeze, you need a special routing algorithm that can follow the contour of the board outline and automatically insert all the signals required. In Xpedition, all curved traces use true arc primitives.
Design Rule Checking (DRC)
Xpedition is unique in its ability to generate and maintain these dynamically and have a DRC that reports if a tear drop fails.
Signal and Power integrity analysis
Co-developed with Xpedition for analysis of flex-rigid designs, HyperLynx understands how interconnects pass different stack-up scenarios and applies proper modelling in each section. You can use this analysis to ensure a functioning design with complex stack-up.
Dive deeper into this topic
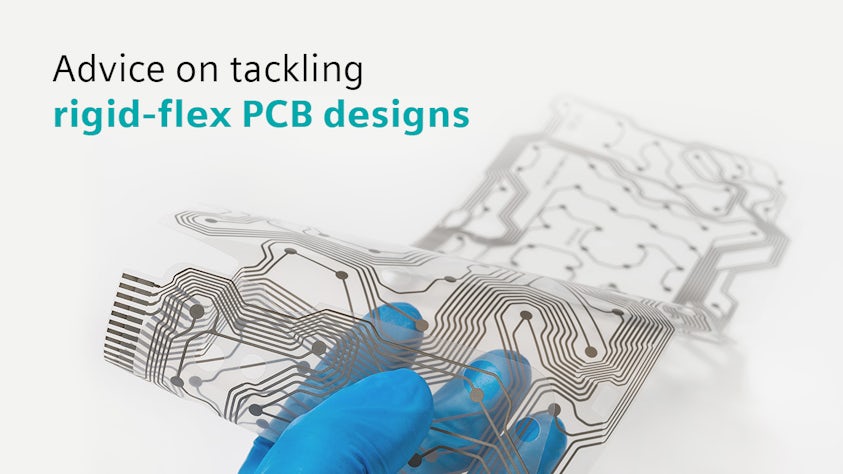
Read more about rigid flex PCB design in our blog: Advice on tackling rigid-flex PCB designs.